Beim Gesenkschmieden können verschiedene Arten von Mängeln auftreten, die sich auf die Qualität Ihres Werkstücks auswirken. FORGE®, eine Simulationssoftware für Warmumformungsprozesse, macht Fehlertests überflüssig, um ein von Anfang an konformes und mängelfreies Werkstück in Bezug auf seine Endgeometrie zu produzieren. Die Simulation ermöglicht die Erkennung von Fertigungsmängeln und ist eine zuverlässige Lösung zur Senkung der Produktionskosten und der Nicht-Qualitätskosten, indem sichergestellt wird, dass die Komponenten den Spezifikationen entsprechen und Stillstandszeiten der Produktionsmaschinen vermieden werden.
Vorhersage von Unterfüllungen
Unterfüllung tritt auf, wenn der Metallfluss einen Abschnitt des Formhohlraums nicht vollständig ausgefüllt hat. Dies liegt vor allem an fehlendem Material oder einer fehlerhaften Matrizenkonstruktion, oder auch an einer ungeeigneten Schmiedetechnik.
Der Ursprung kann mit Hilfe der numerischen Simulation bestimmt werden, um Lösungen zu finden, die das Auftreten dieses Fehlers an Ihrem realen Werkstück vermeiden.
Um Unterfüllungsbereiche mit FORGE® zu identifizieren, kann der Skalar "Kontakt" in der Ergebnisliste ausgewählt werden. Die Unterfüllungsbereiche werden dann am Ende des Fertigungsschritts rot hervorgehoben (Bereich, in dem der Skalar einen positiven Wert hat).
Geschmiedete Kurbelwelle mit Unterfüllungsfehlern.
Reales Werkstück (links), Simulation (Mitte) und Schnittebene (rechts).
Rot markierte Bereiche zeigen die Unterfüllung an.
Eine neue Funktion, die seit FORGE® NxT 3.2 (Dezember 2020) verfügbar ist, ermöglicht es Ihnen außerdem, benutzerdefinierte Aktionsschaltflächen festzulegen und diese mit einem einzigen Klick auf eine Simulation anzuwenden. Diese neue Funktion ermöglicht die Erkennung von Unterfüllungen.
Dank der Schnittebene sind unterfüllte Volumina leicht quantifizierbar, indem der Leerraum zwischen der Matrizenhöhlung und der Metallfront gemessen wird.
Erkennung von Materialfalten und Überlappungen
Diese Art von Fehler tritt auf, wenn zwei Teile des Materials aufeinander treffen. Auch dieser Fehler kann durch fehlendes Material, einer fehlerhaften Matrizenkonstruktion oder einen schlecht kontrollierten Prozess verursacht werden.
Die Simulation kann helfen, diesen Fehler vorherzusehen. In FORGE® steht eine Punktverfolgungsfunktion zur Verfügung, die es ermöglicht, das Auftreten von Falten und Überlappungen im Werkstück leicht zu erkennen. Sie ermöglicht Folgendes:
- Falten in jedem Schmiedeabschnitt zu identifizieren.
- Falten nachzuverfolgen und zu bestimmen, ob sie im Werkstück bleiben oder sich in Richtung Grat bewegen
- Die Tiefe einer Falte zu messen
- Eine Rückwärtsanalyse zu erstellen, um den Ursprung der Falte zu verstehen
Reales Werkstück (Messingfitting - links) und Simulation mit FORGE® (rechts)
Die Punktverfolgung kann in der Werkzeugleiste, unter der Registerkarte "Falten" aktiviert werden, um die Falten in der grafischen Ansicht anzuzeigen. Die roten Punkte zeigen die Bereiche an, in denen das Material mit sich selbst in Kontakt kommt.
Punktverfolgung am Schmiedefall eines Femurschafts
Die automatische Vernetzung von FORGE® sorgt für Präzision in Bezug auf Lage, Größe und Tiefe der Falten.
Vorhersage von Durchflussfehlern
Durchflussfehler treten hauptsächlich am Ende des Schmiedeabschnitts auf. Es besteht dann ein Strömungswettbewerb zwischen Bereichen, in denen das Material blockiert ist (vollständig gefüllter Bereich), und angrenzenden Bereichen, in denen das Material weiterfließt, wodurch dieses Durchflussphänomen entsteht. Dieser Fehler ist besonders heikel, da er auf der Oberfläche des Schmiedeteils nicht erkennbar ist (er wird als Unterhautfehler bezeichnet) und eine zerstörungsfreie Prüfung (Ultraschall) erfordert, um die kritischen Bereiche hervorzuheben. Typischerweise tritt diese Art von Fehler bei Extrusionsprozessen auf, bei denen der Materialfluss Vorwärts- und Rückwärtsstrangpressen kombiniert. Diese Durchflüsse lassen sich in der Regel durch ein Überdenken des Schmiedebereichs und Ändern bestimmter Maße (Durchmesser der Strangpressbereiche, Anstellwinkel, Anschlussradius usw.) beseitigen.
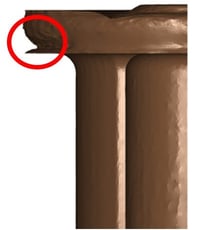
Durch die Simulation dieses Prozesses mit FORGE® können Durchflussfehler mit Hilfe der Markierungsgitterfunktion erkannt werden.
In diesen Extrusionsfällen konnten zwei Durchflussfehler anhand der Markierungsgitterfunktion identifiziert werden: einer auf der Oberseite und der andere in der Ecke. Die Fließgeschwindigkeit des Materials ist in diesen Bereichen nahezu Null.
Vorhersage von fehlerhaften Faserverläufen
Beim Schmieden eines Werkstücks ändert sich durch die Verformung des Metalls die Ausrichtung der Faser. Die Faserlinien sind möglicherweise nicht in der gewünschten Richtung ausgerichtet oder erfüllen nicht die spezifischen Anforderungen, um die mechanische Qualität des Teils zu gewährleisten.
Die numerische Simulation ermöglicht die Modellierung des Faserverlaufs eines Schmiedeteils. Die Markierungsfunktion von FORGE® ermöglicht es, die Entwicklung der Faser zu berechnen und ihre Qualität über den gesamten Verformungsbereich zu beurteilen. Die Konformität des endgültigen Faserverlaufs ist eine Garantie für die Qualität des Schmiedeteils.
Das folgende Beispiel (mit freundlicher Genehmigung des Miguel-Altuna-Instituts in Spanien) zeigt die Entwicklung des Faserverlaufs über eine Reihe von Kaltstauchprozessen. Bei jeder Stufe wird das Werkstück stärker verformt und der Faserverlauf verändert sich.
Die von der FORGE®-Software durchgeführte Berechnung der Markierung zeigt für die endgültige Form die Konformität des Faserverlaufs mit der SAE USCAR8-Spezifikation.
Vermeidung von Rissen
Risse sind Sprünge, die an der Oberfläche oder in der Masse eines Schmiedeteils auftreten können. Sie werden in der Regel durch eine zu abrupte Verformung des Rohlings verursacht. Auch die Qualität des Ausgangsrohlings (Defekte im Zusammenhang mit dem Gießereiprozess: Porositäten, Seigerungen usw.) wird in Frage gestellt, da die auf ein fehlerhaftes Teil ausgeübte Kraft einen Riss verursachen kann.
Das Auftreten von Rissen kann mit Hilfe der Finite-Elemente-Simulation leicht vorhergesagt werden. Die FORGE®-Software modelliert die Metallverformung und den Metallfluss entsprechend Ihrer Prozessparameter, so dass Sie das Fließverhalten während des gesamten Schmiedeprozesses analysieren können. Sie integriert mehrere Beschädigungskriterien, um diese Risse zu vorherzusagen: einige von ihnen sind an die Rheologie gekoppelt wie Lemaitre und andere sind ungekoppelt wie Oyane, Rice & Tracey, Latham & Cockroft, Brozzo, Hill-Devaux, Ghosh, Ayada, Lemaitre 1, 2, 3, 4, 5.
Der Ursprung eines Risses kann mit FORGE® nachvollzogen werden: die Stelle, an der sich der Defekt ursprünglich gebildet hat und wie er sich zu einem Riss entwickelt hat. Die Größe, Tiefe und Ausbreitung des Risses können ebenfalls modelliert werden.
Risse an der Oberfläche
Die FORGE®-Software ermöglicht außerdem die Vermeidung von Mängeln im Zusammenhang mit anderen Umformverfahren wie Strangpressen, Ringwalzen, Querkeilwalzen usw.