Einführung
Der Wachstumsmechanismus der Oxidschicht auf kohlenstoffarmen Stahl wurde in der Literatur eingehend untersucht. Beispielsweise modellierten Yue et al. die Kopplung von mechanischer Belastung und Oxidation1. Analysiert wurde in dieser Studie die gekoppelte Wirkung einer Belastung sowie einem dreistufigen Oxidationsprozess unter isothermen Bedingungen. Hierbei wurden die Stufen wie folgt skizziert:
- Der Sauerstoff wird von der Masse des oxidierenden Gases zur Grenzfläche von Gas und Oxid transportiert, wo er adsorbiert wird;
- Der adsorbierte Sauerstoff wird dann durch die Oxidschicht zum Substrat transportiert;
- An der Grenzfläche von Oxidschicht und Substrat finden Reaktionen statt, um neues Oxid zu bilden.
Das Wachstum der Oxidschicht während der Wärmebehandlung ist ein wichtiger Faktor für die Leistungsfähigkeit und Langlebigkeit von zahlreichen Stahlanwendungen, insbesondere in der Luft- und Raumfahrt. Das Wachstum der Oxidschicht führt zu einem Verlust der ursprünglich vorhandenen Materialien eines Bauteils. Dies ist auf die Reaktion der Ionen auf der Stahloberfläche (z. B. Eisenionen) mit dem in der Atmosphäre vorhandenen Sauerstoff zurückzuführen. Darüber hinaus verändert die Oxidation die mechanischen und thermischen Eigenschaften der Oberfläche eines Bauteils, wodurch sich das Risiko eines strukturellen Fehlers erhöht. Somit hat eine vorhandene Oxidschicht in der Tat während des Bearbeitungsschrittes einen starken Einfluss auf die Reibungsbedingungen an der Schnittstelle zwischen dem Bauteil und dem Schmiedewerkzeug3. Zudem beeinflusst sie auch den Wärmeaustausch zwischen Bauteil und seiner Umgebung oder zwischen Bauteil und Werkzeugen. Dies kann beispielsweise den Wärmeübergangskoeffizienten4 einer Grenzfläche (Oxid/Gesenkoberfläche), den Emissionsgrad5, die Wärmeleitfähigkeit6 oder den Wärmeausdehnungskoeffizienten betreffen. Diese Parameter können auch innerhalb der Oxidschicht von einer Teilschicht zur anderen variieren, je nach ihrer Zusammensetzung.
Aus struktureller Sicht werden in der Literatur drei Hauptbestandteile der Oxidschicht genannt, die in unterscheidbaren Teilschichten angeordnet sind. So bilden sich mit zunehmender Sauerstoffkonzentration in der Schicht nacheinander die Teilschichten Wüstit (FeO), Magnetit (Fe₃O₄) und Hämatit (Fe₂O₃). Wüstit hat in der Regel die geringste Härte, weit unter Fe₂O₃ und Fe₃O₄. Es ist zudem bei hohen Temperaturen weniger stabil, da es leicht mit Sauerstoff reagiert und Fe₂O₃ oder Fe₃O₄ bildet. Magnetit entsteht bei niedrigen Temperaturen direkt durch die Oxidation von Eisen und bei hohen Temperaturen indirekt durch die Oxidation von Wüstit. Hämatit weist gegenüber Magnetit und Wüstit eine höhere elastische Rückgewinnung auf. Es hat von allen drei Phasen die höchste Steifigkeit, gefolgt von Magnetit und Wüstit. Ein gründlicher Vergleich der Eigenschaften aller drei Phasen wird in den Studien von V. Claverie7 vorgestellt. So variiert die Struktur der Unterschichten je nach der Art der Atmosphäre. Die Anteile der einzelnen Unterschichten in der Oxidschicht werden in der Literatur quantifiziert3,8-11. Auch wenn über den Einfluss der oxidierenden Atmosphäre auf die Kinetik des Oxidwachstums in Studien berichtet wurde12-14, erlauben die Ergebnisse keinen präzisen Vergleich der Struktur von Oxidschichten unter Einbezug verschiedener oxidierender Atmosphären, insbesondere unter industriellen Bedingungen.
Dies unterstreicht, wie wichtig es ist, das Wachstum von Oxidschichten auf der Oberfläche von Stahlbauteilen vorherzusehen, insbesondere wenn diese hohen Temperaturen und einer oxidationsfördernden Umgebungen ausgesetzt sind.
In diesem Artikel gehen wir auf eine mitreißende Zusammenarbeit zwischen unserem Team und LISI AEROSPACE ein. Diese zielt auf die Übertragung experimenteller Erkenntnisse in numerischen Modellen ab, die die Bildung von Oxidschichten und einen Bruch während eines Verformungsprozesses auf der Grundlage realer industrieller Parameter vorhersagen können. Die daraus resultierenden Modelle werden in unserer robusten FORGE®-Lösung implementiert und ebnen den Weg für neue und vielversprechende Funktionen.
Experimentelles Verfahren
Ziel war es, den Einfluss der Atmosphäre auf die Oxidationskinetik besser zu verstehen. Untersucht wurden dementsprechend der Einfluss der Wärmebehandlungstemperatur, der Aufrechterhaltungsdauer, der Zusammensetzung des Stahl und des Typs des Ofens. Es wurden verschiedene kohlenstoffarme Stahlsorten verwendet: C22, C45, 34CrMo4 und 42CrMo4. Die Proben wurden unter verschiedenen Bedingungen wärmebehandelt, einschließlich der Variation von Temperatur und Haltedauer. Vorgenommen wurde dies sowohl in einem industriellen Gasofen, der Methan verbrennt, als auch in einem widerstandsbeheizten Elektroofen. Dieser Ansatz ermöglicht es uns, bei den Proben den Einfluss der oxidierenden Atmosphäre auf die Kinetik des Wachstums der Oxidschicht zu untersuchen. So entstehen bei der Verbrennung im Gasofen Kohlenmonoxid (CO) und Kohlendioxid (CO2), während Sauerstoff (O2) als wichtigstes Element des Oxidationsmechanismus verbraucht wird. Dementsprechend sind diese Gase in einem Gasofen in größeren Mengen vorhanden als in einem Elektroofen. Zudem tragen sie zum Wachstumsmechanismus der Oxidhaut bei und führen zu Potenzialunterschieden zwischen den in den beiden Öfen gebildeten Oxidschichten.
Anschließend wurde die Brüche von Oxidschichten untersucht, indem Heißverformungsprozesse mit einer Kamera mit 25 fps aufgezeichnet wurden. Durch die Verknüpfung der Bildauswertung mit der Finite-Elemente-Simulationssoftware FORGE® können die Ereignisse, die zu einem Bruch führen, mit effektiven mechanischen Verformung und Dehnungsraten korreliert werden.
Ergebnisse und Diskussion
Nach der Wärmebehandlung wurde die Oxidschicht durch Kugelstrahlen von der Stahlprobe getrennt. Die Oxidfragmente wurden anschließend mit Hilfe von Lichtmikroskopie und Rasterelektronenmikroskopie charakterisiert. Dabei zeigte sich bei den in beiden Öfen gewachsenen Proben eine Schichtstruktur aus Wüstit (FeO), Magnetit (Fe₃O₄) und Hämatit (Fe₂O₃). Die Anteile der verschiedenen Teilschichten unterscheiden sich jedoch je nach Art des verwendeten Ofens. Im Gasofen besteht die Oxidschicht zu 90 % aus FeO, zu 8 % aus Fe₃O₄ und zu 2 % aus Fe₂O₃. Dies stimmt mit den in der Literatur veröffentlichten Ergebnissen überein3,7-10. Im Elektroofen hingegen enthielten die Oxidschichten an der Grenzfläche von Oxid und Luft weniger als 50 % FeO, einen erheblichen Anteil Fe₃O₄ (~39 % für 34CrMo4) und eine feine Schicht Fe₂O₃ (~9 % für 34CrMo4). Während in der Literatur von einem FeO-freien Oxidumfang, der in einer Atmosphäre von O2+N2 gewachsen ist, sowie von einem Oxidumfang, der ausschließlich aus FeO besteht und in einer Atmosphäre von 100 % CO2 (idem für 15 % CO2 - 85 % N2)12 gewachsen ist, berichtet wird, kommt man zu dem Schluss, dass der Gasofen hauptsächlich die Bildung von Wüstit und dagegen der Elektroofen das Wachstum der anderen Bestandteile begünstigt. Dies lässt sich durch den geringen Sauerstoffgehalt in der Gaskammer des Ofens erklären, der die Bildung sauerstoffreicher Oxide wie Magnetit erschwert.
Die Oxidationskinetik wurde nachfolgend für jede behandelte Probe bewertet, in dem die Massendichte der Oxidhaut pro Flächeneinheit gemessen wurde. Die nachstehende Abbildung zeigt die Massendichten, die in beiden Öfen für verschiedene Stahlsorten gemessen wurden. Insgesamt nimmt die Wachstumskinetik mit der Temperatur zu, und die nominale Zusammensetzung des Stahls scheint einen mehr oder weniger vernachlässigbaren Einfluss auf die Oxidationskinetik zu haben. Auf der Grundlage der experimentellen Ergebnisse haben wir dann ein Kinetikmodell entwickelt, das zur Vorhersage des oxidationsbedingten Massenverlustes dient. Dieses Modell verwendet denselben Formalismus wie die kinetischen Konstanten zur Vorhersage des Massengewinns. Es spiegelt den diffusiven Charakter der Oxidationsreaktion wider, der einem Gleichgewicht zwischen der Diffusion von Eisen- und Sauerstoffionen durch die Oxidschicht entspricht15. Anschließend wurde ein Kalibrierungsschritt durchgeführt, um die für die Kalibrierung des kinetischen Gesetzes erforderlichen Terme zu erhalten. Letzteres wurde dann auf die experimentellen Fälle angewandt, um den Massenverlust vorherzusagen, wie in der Abbildung unten dargestellt. Es ist eine gute Übereinstimmung der Vorhersagen mit den experimentellen Ergebnissen zu erkennen.
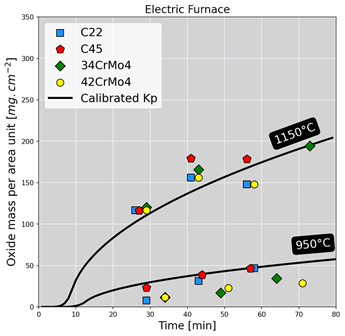
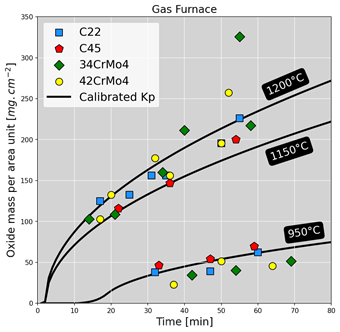
Anwendung des kalibrierten kinetischen Gesetzes auf experimentelle Fälle für beide Arten von Öfen. Die durchgezogenen Linien und die farbigen Muster stellen das Vorhersagemodell beziehungsweise die experimentellen Ergebnisse dar.
Anschließend wurde eine Benutzervariable zur Vorhersage der Oxidationskinetik in die FORGE®-Datenbank für Benutzergesetze implementiert. Im Vergleich zu experimentellen Messungen werden zufriedenstellende Vorhersagen zum Massenverlust erzielt (siehe Abbildung unten), wobei ein unbekannter Messfehler und die im simulierten Beispiel angenommene vereinfachte Wärmebehandlung berücksichtigt werden.
Durée | t = 1500 s | t = 2100 s | t = 3000 s |
Δm mesurée | 132 mg.cm-2 | 156.07 mg.cm-2 | 195.35 mg.cm-2 |
Δm prédite | 115.71 mg.cm-2 | 151.65 mg.cm-2 | 193.44 mg.cm-2 |
Vergleich zwischen Vorhersagen durch FORGE® und experimentellen Ergebnissen für die Stahlsorte C22 unter Verwendung kalibrierter Parameter.
Unsere zweite Motivation bestand darin, den Bruch von Oxidschichten während der Warmverformung zu untersuchen sowie ein Modell zur Vorhersage des Werkzeugverschleißes zu erstellen. Mittels Durchführung zahlreicher Versuche mit einer Warmpresse (hydraulische Presse) wurden die Oxidausfälle mit einer Hochpräzisionskamera aufgezeichnet, um die Ereignisse eines Oxidbruchs zu erfassen (siehe Animation unten). Es wurde eine Methode entwickelt, die Bildanalyse und maschinelles Lernen kombiniert, um ein kritisches Kriterium zu erstellen, das die Ausdehnung der Knüppeloberfläche und die Scherspannung an der Grenzfläche von Metall und Oxid berücksichtigt.
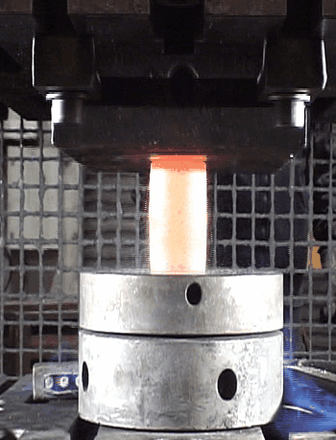
Aufnahmen der Oxidbruchereignisse während eines Heißkompressionstests.
Die entwickelte Methode besteht in der Verarbeitung von Bildern, die während des Warmschmiedens der Probe zur Verfolgung der Probenhöhe als Funktion der Zeit aufgenommen wurden. Daraus ergibt sich der experimentelle Schmiedeplan, der in der FEM-Simulationssoftware FORGE® nachgebildet wurde, Mit diesem wird die Verformungsrate sowie die Dehnung überall auf der Probenoberfläche abgeschätzt, was in der Animation unten zu sehen ist. Es wurden KI-Tools entwickelt, um die wahren Konturen des Knüppels zu identifizieren und die Fehlerstellen zu bestimmen. Die Bruchstelle wurde dann mit dem Zustand der lokalen Verformung und der damit verbundenen momentanen Dehnungsrate in Beziehung gesetzt. Anschließend wurde die Adhäsionsenergie der Oxidschicht in Abhängigkeit von der Dehnungsrate, der Temperatur und der Zunderdicke berechnet.
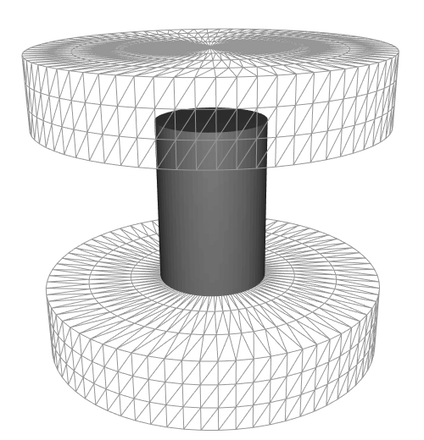
Simulation des Bruchs des Oxids (grau dargestellt) während eines Heißdruckversuchs, erstellt mit der FEM-Simulationssoftware FORGE®.
Schlussfolgerung
Diese Untersuchungen haben zur Entwicklung neuer Funktionen in der Simulationssoftware FORGE® geführt. Diese ermöglichen die Vorhersage der Oxidmassendichte und der Massenbilanz des Materialverlustes während des Warmschmiedeprozesses sowie den Bruch der Oxidhaut an kritischen Dehnungspunkten.
Durch eine proaktive Auseinandersetzung mit den Oxidationsprozessen können die Hersteller dank der Simulationen den Materialverlust vorhersagen und ihn bei der Festlegung des Anfangsgewichts des Knüppels berücksichtigen, wodurch die Maßspezifikationen eingehalten werden. Darüber hinaus ermöglicht das Verständnis der Oxidation die Vorhersage von strukturellen Veränderungen in Bauteilen, die während der Wärmebehandlung und des Schmiedeprozesses verformt werden.
References
- Yue, M., Dong, X., Fang, X. & Feng, X. Effect of interface reaction and diffusion on stress-oxidation coupling at high temperature. Journal of Applied Physics 123, 155301 (2018).
- Deal, B. E. & Grove, A. S. General Relationship for the Thermal Oxidation of Silicon. Journal of Applied Physics 36, 3770–3778 (1965).
- Munther, P. A. & Lenard, J. G. The effect of scaling on interfacial friction in hot rolling of steels. Journal of Materials Processing Technology 88, 105–113 (1999).
- Hu, P., Ying, L., Li, Y. & Liao, Z. Effect of oxide scale on temperature-dependent interfacial heat transfer in hot stamping process. Journal of Materials Processing Technology 213, 1475–1483 (2013).
- Fong, R. W. L., Paine, M. & Nitheanandan, T. Total hemispherical emissivity of pre-oxidized and un-oxidized ZR-2.5NB pressure-tube materials at 600 °c to 1000 °c under vacuum. CNL Nuclear Review 5, 85–93 (2016).
- Beygelzimer, E., Beygelzimer, Y. & Llc, O.-E. Thermal conductivity of oxide scale and its components in the range from 0 °C to 1300 °C: generalized estimates with account for movability of phase transitions.
- Claverie, Vi. Study of the thermo-mechanical and fracture behaviour of iron oxide scales at room temperature and at high temperature. Diss. Université Paris sciences et lettres (2023).
- De la Garza, M., Artigas, A., Monsalve, A. & Colás, R. Modelling the Spalling of Oxide Scales During Hot Rolling of Steel Strip. Oxid Met 70, 137–148 (2008).
- Chen, R. Y. & Yuen, W. Y. D. Review of the High-Temperature Oxidation of Iron and Carbon Steels in Air or Oxygen.
- Caplan, D., Sproule, G. I., Hussey, R. J. & Graham, M. J. Oxidation of Fe-C alloys at 700 °C. Oxid Met 13, 255–272 (1979).
- Sheasby, J. S., Boggs, W. E. & Turkdogan, E. T. Scale growth on steels at 1200°C: rationale of rate and morphology. Metal Science 18, 127–136 (1984).
- Abuluwefa, H., Guthrie, R. I. L. & Ajersch, F. The effect of oxygen concentration on the oxidation of low-carbon steel in the temperature range 1000 to 1250°C. Oxid Met 46, 423–440 (1996).
- Abuluwefa, H. T., Guthrie, R. I. L. & Ajersch, F. Oxidation of low carbon steel in multicomponent gases: Part I. Reaction mechanisms during isothermal oxidation. Metall and Mat Trans A 28, 1633–1641 (1997).
- Pettit, F., Yinger, R. & Wagner, J. B. The mechanism of oxidation of iron in carbon monoxide-carbon dioxide mixtures. Acta Metallurgica 8, 617–623 (1960).
- Wagner, C. Equations for transport in solid oxides and sulfides of transition metals. Progress in Solid State Chemistry 10, 3–16 (1975).