Introduction
The growth mechanism of the oxide scale on low-carbon steels has been extensively studied in literature. For example, in Yue et al. the coupling effect of mechanical stress to oxidation was modeled1. This study analyzed the coupled effect of stress and a three-stage oxidation process under isothermal conditions, with the stages outlined as follows:
- the oxygen is transported from the bulk of the oxidizing gas to the gas/oxide interface, where they are adsorbed;
- the adsorbed oxygen is transported across the oxide film towards the substrate; and
- reactions take place at the oxide film/substrate interface to form new oxide.
A general equation for oxidation kinetics was established. This model was then verified by comparing oxide layer thicknesses predicted by the model, with those of oxide layers formed on substrates placed in a quartz-based oxidation tube, into which dry, purified oxygen is introduced2. However, these oxidation conditions are far from those encountered in an industrial environment, as they are unable to replicate an atmosphere similar to that found in industrial furnaces, such as gas or electric furnaces.
Oxide scale growth during heat treatment is an important factor in the performance and longevity of steels in many applications, notably in aerospace. The growth of the oxide layer results in the loss of materials initially present in the part, due to the reaction of ions on the steel surface (e.g. iron ions) with oxygen present in the atmosphere. In addition, oxidation modifies the mechanical and thermal properties of the part's surface, increasing the risk of structural failure. In fact, the presence of an oxide layer has a strong impact on friction conditions at the interface between the part and the forging tool during processing steps3. It also affects thermal exchanges between the part and its environment, or between the part and the tools. This may concern, for example, the interfacial (oxide/die surface) heat transfer coefficient4, emissivity5, thermal conductivity6 or the thermal expansion coefficient. These parameters can also vary within the oxide layer from one sub-layer to another, depending on its composition.
From a structural point of view, the literature reports three main constituents of the oxide layer arranged in distinguishable sublayers. As the oxygen concentration of the layer increases, the sublayers formed are successively wüstite (FeO), magnetite (Fe₃O₄) and hematite (Fe₂O₃). Wüstite tends to have the lowest hardness, well below Fe2O3 and Fe3O4, and is less stable at high temperatures as it reacts easily with oxygen to form Fe2O3 or Fe3O4. Magnetite is directly formed at low temperature from Fe oxidation, and indirectly at high temperature from the oxidation of wüstite. Hematite exhibits higher elastic recovery than magnetite and wüstite. It is the stiffest of the three phases, followed by Magnetite, and Wüstite. A thorough comparison of the properties of the three phases is presented in the studies conducted by V. Claverie7. This sub-layer structure varies according to the nature of the atmosphere. The proportions of each of the sublayers in the oxide layer are quantified in the literature3,8-11. Although the influence of the oxidizing atmosphere on oxide growth kinetics has been reported12-14, the results of these studies do not allow rigorous comparison of the structure of oxide layers obtained in different oxidizing atmospheres, particularly under industrial conditions.
This underscores the importance of anticipating the growth of oxide layers on the surface of steel components exposed to high temperatures and oxidation-promoting environments.
In this article, we explore an exciting collaboration between our team and LISI AEROSPACE, aimed at translating experimental findings into numerical models that can predict the formation of oxide layers and their failure during deformation processes, based on real-world industrial parameters. The resulting models are implemented in our robust FORGE® solution, paving the way for new and promising features.
Experimental procedure
With the goal of better understanding the impact of the atmosphere on oxidation kinetics, the influence of heat treatment temperature, maintain duration, steel composition and the type of furnace was investigated. Different low-carbon steel grades were employed: C22, C45, 34CrMo4 and 42CrMo4. These samples underwent heat treatment under diverse conditions, including variation of temperature and holding duration, using an industrial gas furnace that combusts methane and a resistance-heated electric furnace. This approach allows us to examine the influence of the oxidizing atmosphere on the kinetics of oxide layer growth on the samples. In fact, the combustion process in the gas furnace produces carbon monoxide (CO), and carbon dioxide (CO2), while consuming oxygen (O2), the main element involved in the oxidation mechanism. These gases are therefore present in greater quantities in the gas furnace than in the electric furnace. They contribute to the growth mechanism of the oxide scale, leading to potential differences between the oxide layers formed in the two furnaces.
Oxide scale failure was then studied by capturing hot-deformation processes using a 25-fps camera. Associating image exploitation with the Finite Element (FEM) simulation software FORGE® enables to correlate the failure events with effective mechanical deformation and strain rates.
Results and discussion
Following the heat treatment, the oxide scale was separated from the steel sample by shot peening. Fragments of oxide were then characterized with optical microscopy and scanning electron microscopy, showing a layered structure of wüstite (FeO), magnetite (Fe3O4) and hematite (Fe2O3) for samples grown in both furnaces. However, the proportions of various sublayers differ according to the furnace used. For the gas furnace, the oxide scale consists of 90% of FeO, 8% of Fe3O4 and 2% of Fe2O3 which aligns with the results reported in literature3,7-10. On the other hand, for the electric furnace, the oxide layers contained less than 50% of FeO, a significative portion of Fe3O4 (~39% for 34CrMo4) and a fine layer of Fe2O3 (~9% for 34CrMo4) at the oxide/air interface. While the literature reports an FeO-free oxide scale grown in an atmosphere of O2+N2, and an oxide scale formed solely of FeO grown in an atmosphere of 100% CO2 (idem for 15% CO2 – 85% N2)12, it is concluded that the gas furnace mainly favors the formation of wüstite, and that conversely, the electric furnace favors the growth of the other constituents. This can be explained by the low oxygen content in the gas furnace chamber, which makes it more difficult for oxygen-rich oxides such as magnetite to form.
Oxidation kinetics were then assessed by measuring the mass density of the oxide scale per unit area for each sample treated. The figure below shows the mass densities measured in both furnaces for different steel grades. Overall, growth kinetics increase with temperature, and the nominal composition of steel seems to have a more or less negligible effect on oxidation kinetics. Based on the experimental results, we then developed a kinetics model that serves to predict mass loss due to oxidation. This model uses the same formalism as the kinetic constants for predicting mass gain, reflecting the diffusive character of the oxidation reaction corresponding to an equilibrium between the diffusion of iron ions and oxygen ions through the oxide layer15. A calibration step was then carried out to obtain the terms needed to calibrate the kinetic law. The latter was then applied to the experimental cases to predict mass loss, as illustrated in the figure below. A good agreement of predictions with experimental results can be seen.
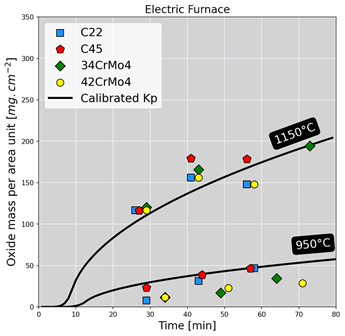
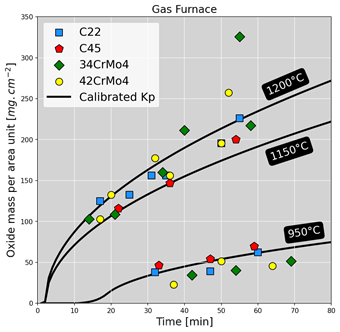
Application of the calibrated kinetic law to experimental cases for both types of furnaces. The solid lines and colored patterns represent respectively the predictive model and experimental results.
A user variable for predicting oxidation kinetics was then implemented in the FORGE® user law database. Satisfactory mass loss predictions are obtained compared to experimental measurements (see figure below), taking into account the unknown measurement error and the simplified heat treatment considered in the simulated example.
Duration | t = 1500 s | t = 2100 s | t = 3000 s |
Measured Δm | 132 mg.cm-2 | 156.07 mg.cm-2 | 195.35 mg.cm-2 |
Predicted Δm | 115.71 mg.cm-2 | 151.65 mg.cm-2 | 193.44 mg.cm-2 |
Comparison between FORGE® predictions and experimental results for the C22 grade steel using calibrated parameters.
Our second motivation was to investigate the oxide scale failure during hot deformation and build a model to anticipate the tool wear. By performing numerous hot-compression tests (hydraulic press), the oxide failures were recorded using a high precision camera to capture the oxide break events (see animation below). A method combining Image Analysis and Machine Learning has been developed to build a critical criterion which considers the billet surface expansion, and the shear stress at the metal/oxide interface.
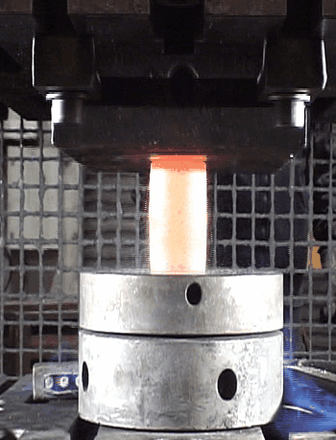
Captured images of the oxide break events during a hot compression test.
The method consists of treating images captured during sample hot forging to follow the sample height as a function of time. This yields to the experimental forging schedule which was reproduced in the FEM simulation software FORGE® to estimate the deformation rate and the strain anywhere on the sample surface as can be seen in the animation below. AI tools have been developed to identify the true billet contours and estimate failure locations. The failure location was then related to its state of the local deformation as well as the associated instantaneous strain rate. Adhesion energy of the oxide layer dependent on strain rate, temperature, and scale thickness, was then calculated.
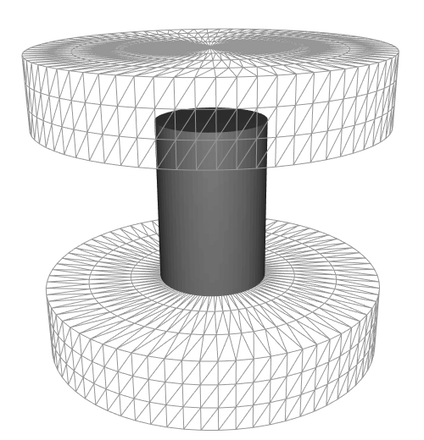
Simulation of the oxide (represented in grey) failure during a hot compression test, obtained using the FEM simulation software FORGE®.
Conclusion
These investigations have led to the design of new functionalities in the simulation software FORGE® to permit the prediction of the oxide mass density and the mass balance of wasted material along hot forging processes, as well as oxide scale failure at critical strain points.
By proactively addressing the oxidation processes, manufacturers can predict material loss thanks to simulations and consider it in the definition of the initial weight of the billet, thereby maintaining dimensional specifications. Additionally, understanding oxidation allows for the prediction of structural changes in components that undergo deformation during thermal treatment and forging processes.
References
- Yue, M., Dong, X., Fang, X. & Feng, X. Effect of interface reaction and diffusion on stress-oxidation coupling at high temperature. Journal of Applied Physics 123, 155301 (2018).
- Deal, B. E. & Grove, A. S. General Relationship for the Thermal Oxidation of Silicon. Journal of Applied Physics 36, 3770–3778 (1965).
- Munther, P. A. & Lenard, J. G. The effect of scaling on interfacial friction in hot rolling of steels. Journal of Materials Processing Technology 88, 105–113 (1999).
- Hu, P., Ying, L., Li, Y. & Liao, Z. Effect of oxide scale on temperature-dependent interfacial heat transfer in hot stamping process. Journal of Materials Processing Technology 213, 1475–1483 (2013).
- Fong, R. W. L., Paine, M. & Nitheanandan, T. Total hemispherical emissivity of pre-oxidized and un-oxidized ZR-2.5NB pressure-tube materials at 600 °c to 1000 °c under vacuum. CNL Nuclear Review 5, 85–93 (2016).
- Beygelzimer, E., Beygelzimer, Y. & Llc, O.-E. Thermal conductivity of oxide scale and its components in the range from 0 °C to 1300 °C: generalized estimates with account for movability of phase transitions.
- Claverie, Vi. Study of the thermo-mechanical and fracture behaviour of iron oxide scales at room temperature and at high temperature. Diss. Université Paris sciences et lettres (2023).
- De la Garza, M., Artigas, A., Monsalve, A. & Colás, R. Modelling the Spalling of Oxide Scales During Hot Rolling of Steel Strip. Oxid Met 70, 137–148 (2008).
- Chen, R. Y. & Yuen, W. Y. D. Review of the High-Temperature Oxidation of Iron and Carbon Steels in Air or Oxygen.
- Caplan, D., Sproule, G. I., Hussey, R. J. & Graham, M. J. Oxidation of Fe-C alloys at 700 °C. Oxid Met 13, 255–272 (1979).
- Sheasby, J. S., Boggs, W. E. & Turkdogan, E. T. Scale growth on steels at 1200°C: rationale of rate and morphology. Metal Science 18, 127–136 (1984).
- Abuluwefa, H., Guthrie, R. I. L. & Ajersch, F. The effect of oxygen concentration on the oxidation of low-carbon steel in the temperature range 1000 to 1250°C. Oxid Met 46, 423–440 (1996).
- Abuluwefa, H. T., Guthrie, R. I. L. & Ajersch, F. Oxidation of low carbon steel in multicomponent gases: Part I. Reaction mechanisms during isothermal oxidation. Metall and Mat Trans A 28, 1633–1641 (1997).
- Pettit, F., Yinger, R. & Wagner, J. B. The mechanism of oxidation of iron in carbon monoxide-carbon dioxide mixtures. Acta Metallurgica 8, 617–623 (1960).
- Wagner, C. Equations for transport in solid oxides and sulfides of transition metals. Progress in Solid State Chemistry 10, 3–16 (1975).