Was ist das Druckgussverfahren?
Druckguss, (HPDC: High Pressure Die Casting auf Englisch) ist ein Verfahren, das die Herstellung von Präzisionsteilen in großen Serien zu relativ geringen Kosten ermöglicht, da es leicht automatisiert werden kann.
Genauer gesagt besteht dieser Prozess nach dem Eingießen des Metalls in die Kammer aus 3 Phasen:
- Eine erste Phase mit niedriger Geschwindigkeit, in der das Metall bis zu den Gussanschnitten in die Kammer gedrückt wird.
- Eine zweite Phase mit Hochgeschwindigkeitseinspritzung in den Formhohlraum.
- Und schließlich eine dritte Phase, in der der Kolben während des gesamten Erstarrungsprozesses einen konstanten Druck aufrechterhält.
Im Gegensatz zum Niederdruckguss erfolgt die Einspritzung nicht unbedingt senkrecht vom Boden der Form aus.
Modellierung der einzelnen Teile des Druckgussverfahrens zur Herstellung eines Gehäuses: Endteil (in grau), Formen, Kerne, Kolben, Stange… Mit freundlicher Genehmigung der Renault Group
Vorteile des Druckgussverfahrens
Dieses Verfahren ist für seine hohe Präzision anerkannt und garantiert eine hochwertige Fertigung für sehr dünne oder komplex geformte Teile. Daher wird der Begriff "near-net-shape manufacturing" verwendet, um das Druckgussverfahren zu definieren.
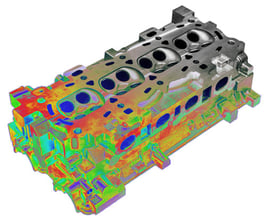
Das Verfahren wird häufig zur Herstellung von Teilen aus Leichtmetalllegierungen wie Aluminium, aber auch aus Zinklegierungen (Zamak usw.) und Magnesium verwendet und eignet sich aufgrund seiner Schnelligkeit besonders gut für die automatisierte und großvolumige Produktion und gewährleistet eine gleichbleibende Qualität der Teile. Es wird daher hauptsächlich in der Automobilindustrie zur Herstellung von Aluminiumgehäusen (Motor, Kupplung, usw.) eingesetzt. Auch andere Branchen wie die Elektronik-, Medizin-, Sport-, Luxusgüter- und Bauindustrie nutzen den Druckguss für die Herstellung von Hydraulikkomponenten aus Zinklegierungen oder Strukturteilen aus Magnesiumlegierungen.
Allerdings weisen die produzierten Teile aufgrund der sehr schnellen Erstarrungsraten oft mehr Porosität auf als beim Sand- oder Kokillenguss. Außerdem werden Fehler nicht immer durch die Wirkung des Kolbendrucks in Phase 3 kompensiert. Diese können aber mit Hilfe der digitalen Simulation vorweggenommen werden.
Prädiktive Simulation des Druckgussverfahrens
Die auf Gießereiprozesse ausgerichtete Software THERCAST® ermöglicht eine präzise und vorausschauende Analyse des Druckgussprozesses, vom Füllen bis zur Erstarrung:
- Konfiguration sämtlicher Prozessparameter: Geometrien der Werkzeugkomponenten, Materialien, Betriebstemperaturen, Druckverlauf, Wärmeaustausch- und Schlichtbereiche, Kühlkanäle...
- Modellierung aller Phasen des Prozesses: Aufheizen der Form, Füllen der Kammer mit einem Becher, Bewegung des Kolbens, Aufsteigen des Metalls in der Form und Halten, Kühlmittelumlauf, Auswurf des Teils
- Visualisierung des Metallflusses und Berücksichtigung seiner Auswirkungen
- Visualisierung der Metallschrumpfung während der Erstarrung
Entwicklung der Metallfront bei der Herstellung eines Druckgussgehäuses
- Vorhersage von Fehlern: primäre und sekundäre Schrumpfungen, Einschlüsse, Spannungsrisse, Fehlmengen und Mängel, usw.
- Überwachung der Luftblasen
- Analyse der Formen: Temperatur und Verformung, reale Kinematik der beweglichen Teile
- Metallurgische Entwicklung: Flüssig/Fest-Phasenverteilung, Wachstum und Ausrichtung der Körner, Mikro- und Makroseigerungen
- Optimierung der Zykluszeit entsprechend der Gestaltung des Teils
- Optimierung des Anschnittbereichs
Erkennung von Porosität im Teil
THERCAST®-Funktionen für den Druckguss
- Simulations-Template für den Druckguss
- Kopplung von Strömungsmechanik und Festkörpermechanik während der gesamten Berechnung
- Parallelisierung der BerechnungP für eine höhere Geschwindigkeit der Ausführung
- Start einer vollständigen thermomechanischen Analyse für eine hohe Genauigkeit der Ergebnisse
- Gekoppelte thermomechanische Auflösung im Teil und in allen Komponenten der Form (einschließlich Einsätze und Stifte) zur Vorwegnahme von Verformungen
- Optimierung des Zuführsystems für Gewichts- und Laufleistungssteigerungen
- Komplette metallurgische Analyse
- Materialdatenbank und eigener Erstellungsbereich
- Konfiguration von ZTU-Diagrammen (Zeit-Temperatur-Umwandlung)
- Export von THERCAST®-Ergebnissen in andere Berechnungs- oder Finite-Elemente-Software
- Perfekte Interoperabilität mit der SIMHEAT®-Software, die die Simulation der Wärmebehandlung von Teilen nach dem Gießen ermöglicht.
- Überwachung der Einschlüsse während des gesamten Prozesses. >Mehr erfahren
- Perfekte Simulation der Temperaturwechsel für eine realitätsnahe Betrachtung der Auswirkungen.
Hauptvorteile von THERCAST®
THERCAST® verfügt über mehrere Funktionalitäten, die es ermöglichen, die Genauigkeit der Berechnungsergebnisse zu erhöhen und die Herstellungskosten der im Druckgussverfahren hergestellten Teile zu reduzieren:
- Die Simulation "Füllen und Erstarrung" wird zu jedem Zeitpunkt mit einer einzigen Software durchgeführt: die Berechnungen "Strömungsmechanik" und "Festkörpermechanik" sind vollständig integriert.
- THERCAST® verfügt über ein evolutives Kontaktmanagement zur Erkennung einer eventuellen Ablösung zwischen dem Gussmetall und der Form. Sobald die Schrumpfung auftritt, berücksichtigt die Software den Einfluss des Luftspalts und passt den Wärmeaustausch zwischen Metall und Form lokal an.
- Es ist möglich, die thermische und mechanische Auflösung zu koppeln und die Berechnungen gleichzeitig durchzuführen. THERCAST® kann daher die Verformung der Form entsprechend der Verformung des Teils modellieren und umgekehrt. Beide Phänomene treten gleichzeitig auf.
- Die Software kann die Spannungen visualisieren, die das Metall unter dem Druck des Kolbens auf die Stifte ausübt. Es ist daher möglich, die Verformung der Form und die möglichen Auswirkungen auf die Geometrie des Teils vorherzusagen.
- Die Studie der Optimierung des Zuführsystems ermöglicht es, die Mindestmaterialmenge, die zur Herstellung des gewünschten Teils erforderlich ist, genau zu definieren.
- Die Prozesseingangsdaten können parametriert werden, um die Menge des einzuspritzenden Metalls zu bestimmen und damit Verluste zu begrenzen. Die Reduzierung des Materialabfalls sorgt für wertvolle Einsparungen im gesamten Fertigungsprozess.
- Die Möglichkeit, den thermischen Zyklus und die Kinematik der Formen zu modellieren erlaubt eine genaue Untersuchung des Druckgussprozesses
- Die Aktionen an den einzelnen Objekten und die Möglichkeit, die Ausstoßreihenfolge der Kerne zu verwalten, tragen zu einer besseren Genauigkeit der Wärmeströme bei.
Befüllen einer Form durch Druckgießen zur Herstellung von Probekörpern
Haben Sie weitere Fragen zu THERCAST®?