Layout of Highly Stressed Injection and Motor Components
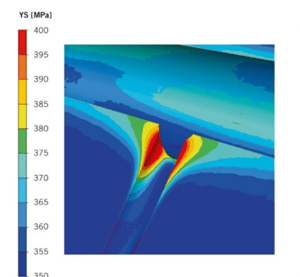
Hydraulic autofrettage technique is a specific process used in the manufacturing of automotive components such as common-rail for Diesel- injection system. These parts are subjected to cyclic stress with very high internal pressures and the autofrettage process is a mean of increasing their fatigue life.
During computational layout of this process step, consideration of anisotropic material behaviour is of primary importance. So far, local quite possibly directional component-strength (such as due to prior autofrettage) has not been taken into account among standards to evaluation of durability for forged components.
Discover our solutionIn the context of a joint development project, this gap has been closed by Hirschvogel Automotive Group, Engineering Center Steyr and Transvalor, in a study mainly done thanks to FORGE®, simulation software for metal forming process. Furthermore, the coupling between the software FORGE® and FEMFAT® is also highlighted in order to assess the fatigue-life resistance of forged components.
This article co-written by Patrice Lasne, Simulation Expert at Transvalor, illustrates the work conducted on the ‘autofrettage’ technique.