Continuous casting is a very difficult process to simulate: it requires computation times long enough to model the entire caster, from the tundish to slab solidification. The simulation is based on a finite elements model that generates increasingly heavy meshing as the length of the casting increases.
To meet this challenge, the THERCAST® software offers three computation methods:
- Global Computation method: computation over the entire length of the casting, giving precise thermomechanical results but requiring longer computation times.
- Slice Computation method: simplified slice computation that reduces computation times, but reserved for thermal computation only.
- Global Slice Computation (GSC) method: a new method which reduces computation times while allowing precise thermomechanical analysis.
Diagram comparing the three computation methods in terms of speed, precision and operability
Significant reduction in computation times and accuracy of results
Each of the computation methods proposed for continuous casting simulation offers advantages depending on the objectives and the type of results the user wishes to obtain.
But the very latest method, which is now an exclusive feature of THERCAST®, is the so-called “Global Slice Computation” (GSC) method. Integrated since 2020 in the THERCAST® NxT 2.0 version, it combines the other two "Global Computation" and "Slice Computation" methods and therefore allows a drastic reduction in computation times (CPU) while maintaining the precision of thermomechanical results.
This method developed by Transvalor's scientific teams is only available in our THERCAST® software.
To better understand the operation and advantages of the GSC approach, it is important to know the three methods offered by THERCAST®.
Global Computation method
The Global Computation method consists in simulating changes to the cast product from the mold outfeed to the end of the secondary cooling area.
It allows a full thermomechanical computation to be performed over the entire length of the cast product. The size of the finite elements model will thus increase as casting progresses.
This method is therefore as precise as possible from a digital resolution standpoint, since all thermophysical phenomena and contact events are taken into account. The only drawback is that it can generate relatively long computation times, especially if the cast length turns out to be significant.
Slice Computation method
The Slice Computation method consists in simulating only one slice of product which will “circulate” from the mold and over the entire cast length.
This is a simplified method that considerably accelerates computation times, but that is generally reserved for thermal computations only. In this case, the software maintains an imposed casting speed at the mold outfeed and applies boundary conditions to the upstream face of the slide (e.g.: adiabatic exchange, imposed pressure).
Global Slice Computation method
The new Global Slice Computation (GSC) method combines the advantages of two previous methods to achieve complete thermomechanical resolution with greatly reduced computation times.
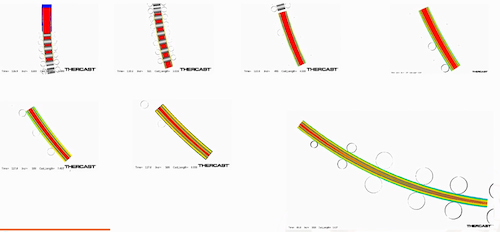
How does the GSC method work?
- The desired cast length is cut into multiple successive sections at strategic user-defined locations.
- At the start of each section, the computation starts with a slice as described in the Slice Computation method.
- This slice then grows along the length of the section as described in the Global Computation method.
- At the end of the section, the software automatically extracts a new slice corresponding to the downstream face of the cast product to reintroduce it into the computation of the next section. This new slice retains all of the previous thermomechanical history and the boundary conditions imposed.
Why does this method reduce computation times?
Thanks to the innovative GSC method, the size of the finite elements model does not constantly increase. At each start of section, the model is reduced to the size of a slice and thus the computation times no longer increase in an almost exponential manner, but rather in a linear manner with cast length. This method represents the best compromise between precision, speed and usability.
By how much can computing times be reduced?
There is no defined reduction in time since the duration of the computation also depends on your process parameters and the desired analysis.
For example, for an industrial case with a cast length of 35 meters, computation times were 10 times shorter with the Global Slice Computation (GSC) method than with the Global Computation method, for the same level of precision of the calculated results.
THERCAST® for a realistic representation of continuous casting
Thanks to the liquid/solid thermomechanical coupling, THERCAST® can faithfully model the continuous casting process, from the tundish to the liquid pool, taking into account the primary and secondary cooling.
Its dedicated interface allows you to configure all the parameters of the caster for a realistic representation of your process: geometry and machine parameters (inputs, rollers, sprays, etc.).
The software also offers features to take into account any type of phenomenon such as deformation in contact with rollers, soft reduction, spray cooling, breakage, etc. Note that our development plan includes the electromagnetic stirring functionality which will be one of the main new features of our next version.