What is ROLLING FOR LONG and flat PRODUCTS?
Rolling is a plastic-deformation shaping operation designed to reduce the section of a long product by passing it between two or more axisymmetric tools rotating around their axis; the tools’ rotation is what drives the product the right way through friction.
Rolling is applied after the metal is made by continuous casting. This process is mainly used to produce strong sheets, beams and rails, some tubes, etc.
Long product rolling with equivalent strain - FORGE® simulation
Computation approaches
Finite element analysis for hot rolling processes remains challenging because various numerical approaches can be used depending on the centres of interest. In FORGE®, two approaches exist: the standard incremental formulation and the new steady-state method. The advantage of using the incremental formulation is to address local shape-defect detection. Using the finite element analysis, it is possible to predict folds, underfill, spread, bowing, end effects and torque.
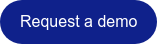
Industrial rolling
Industrial hot rolling configurations, including standard I-beam rolling and the more challenging Kocks rolling mill, can be illustrated using FORGE®. Typical issues such as tail pinching or ripple-like defects can be demonstrated, and control of the tension established between finishing mill stands can be studied to avoid stretching or tearing phenomena.
Benefits OF a Predictive simulation
Simulation provides important information about the entire rolling process. FORGE® provides accurate prediction of:- Shape evolution (profiles) at any time of the process
- Checking product/roll contact: important for understanding the impact that the roll pass has on the product’s profile
- Temperature evolution per pass
- Influence of the roll geometry in each section
- Forces and torques applied on the rolls
- Strain evolution and profiles (centred line)
- Deformation level
- Metallurgical changes such as phase transformation
- Potential defects like laps, hot tearing, cracks, twisting or ripple effects
FORGE® can be used for simulation of the rolling shape and to check the influence of the roll spacing and the heat gradient in the furnace. It allows you to track the evolution of the square to oval shape with considering casting defects evolution and to make comparisons of profiles (Figure 3). It is possible to detect the entry twist and ripples (I-beam).
Influence of roll geometry in each section
Black: current shape / Orange: modified shape
Competitive features of FORGE® Rolling long products
- Contact computation between the product and the rolls is improved thanks to the use of a Nagata smoothing technique in roll discretization. This smoothing technique consists in enriching the linear approximation space with 2nd order functions based on the normal vector continuity argument.
- Bi-mesh is a multi-grid technique that can be applied to reduce the computation time for the rolling simulation while using the standard incremental formulation.
- Coupling with THERCAST® (simulation software for casting applications) can be used to monitor casting defects during the rolling processes.
- When manufacturing long products, it is common to use a series of rolling stands to obtain high production rates. With FORGE®, a MPFX file can be used to set the kinematics of multi-pass processes.
- Using the "Yield Computation" feature, it is possible to use forged parts to determine which maximum part size you can obtain and reduce your material loss. This feature automatically calculates the yield of your long and/or flat sheet metal products and rectangular or round bars manufactured by rolling and cogging.
Yield Computation feature
Case Study - compare blooming and forging process for the manufacturing of steel bars
In order to produce stainless-steel round bars, the Spanish company Tubacex has used FORGE® to analyze the differences observed on load distribution, effective stress, porosity and grain size evolution between a forging and a blooming process.