European Conference on Continuous Casting
Transvalor attended the ECCC 2021, the European Conference on Continuous Casting held in Bari, Italy from 20 to 22 of October.
This conference was organized by AIM (the Italian Association for Metallurgy) since 1991, which organizes various events around metal forming (casting, heat treatment, materials, etc.).
The ECCC 2021 brought together academics and professionals of the continuous casting community in order to share their vision of the future of their activity in terms of process development and new technologies. Various topics have been discussed such as casting technologies, product quality control, numerical simulation, Industry 4.0, etc.
Grégory Puaux, Software Developer at Transvalor, held a conference on:
- Electromagnetic Stirring Simulation with THERCAST®
It is now possible to simulate the electromagnetic stirring with THERCAST®. This new functionality can be activated on ingot casting, foundry casting and continuous casting simulations. The main principle is a coupling between an electromagnetic solver getting induction parameters, temperature and fluid velocity as input and giving heat power and Lorentz forces as results. These two fields are used by the thermohydromechanic solver. In the next major release of the software, the full EMS functionality will be available. In this presentation, we will present some results using a weak coupling scheme (electromagnetic computation is performed once and the results are used during all the thermohydraumechanic computation without update if the material properties or velocities change).
THERCAST® for continuous casting simulation
Steelmakers seek to produce cast parts with high requirements and performance, that’s why they may need to find useful tools such as simulation software to optimize their process.
THERCAST® allows realistic modeling of your continuous casting process, from the filling to the solidification thanks to a liquid/solid thermomechanical coupling. It takes into account dies, inlets, rollers and spray and predicts inclusions, cracks and tears.
The soft reduction model has been improved in THERCAST® NxT 2.0 version. It allows the impact of pinch rollers on the cast product to be analyzed. Then, you can optimize the positioning of the straightening areas and the roller management to improve your product quality.
Visualization of the impact of rollers on the end of the liquid well with THERCAST®
Simulation of soft reduction at ABS Metallurgical Center
ABS Metallurgical Center (France) conducted a study on revamping a continuous casting machine to include soft reduction. They used THERCAST® software to validate the dimensioning of a new ingot shape.
Thank to this study, they were able to control the internal health of products and anticipate the soft reduction impact.
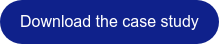