FORGE® Hot Metal Forming ESSENTIAL is suitable for most standard hot forming processes and especially dedicated to closed-die forging. It is designed for process engineers looking for quick, reliable answers to validate their forging layout with a special focus on metal flow, detection of major defects and forging loads.
What's inside?
☑ Hot forging☑ Warm forging
☑ Closed-die forging
☑ Hammer forging
☑ Bar shearing
☑ Flash trimming
☑ Preforming (reducer rolling, cross wedge rolling)
☑ Rigid tooling
☑ Die stress analysis (uncoupled approach)
☑ Material database for hot/warm forging
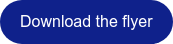
Key Advantages
- 2D and 3D simulations
- Ability to combine all simulations within the same computation chain
- Batch manager capability to launch a series of simulations one after the other
- User-friendly interface with dedicated templates for the forging industry
- Access to a wide variety of forging equipment: hydraulic press, crank press, drop hammer, counterblow hammer, etc.
- Fully automatic and highly adaptive mesh generator
- Automatic report generator
- High parallel scalability (efficiency based on multiple computational cores) for optimal CPU time speedup
- A robust FEM solver delivering highly reliable results
- Exhaustive material database with more than 800 materials specifically characterized for hot forming processes
- Full compatibility with JMatPro® material software
- Grain flow representation within the part, thanks to our efficient marking grid technique. Marking grids are used to track and locate sensitive areas such as sheared billet surfaces or centerline segregation. This technique can also be used to detect folds, laps and flow-through defects
- Use of sensors to track material points, follow their displacement and record scalar information (temperature, strain, etc.). Sensors provide an understanding of the origin of an issue detected on the finished forged product
- Access to damage criteria to anticipate inner or surface cracks
- Tooling & Forging equipment analysis: tonnage, abrasion wear, stress and deflection obtained via uncoupled die analysis
- Microstructure analysis to calculate grain size and the recrystallized fraction for a selection of alloy steels and nickel-based alloys
Your benefits
➽ Simulation of every stage of the forging sequence including (but not limited to) hot shearing of the starting bar, billet transfer from furnace to press, preforming (reducer rolling), upsetting / blocker / finisher operation and final flash trimming. At every step of the process, the software performs an accurate prediction of the metal deformation to anticipate forming issues, control uncertainties on the manufacturing process and, in the end, ensure high-quality forged products.
➽ An accurate prediction of the metal flow, the final part’s dimensions, the press load to forge the component, the grain flow and various kinds of defects such as folds/laps or cracks.
➽ Performing tooling analysis with deep insights into abrasive wear and load balancing in case of multiple impression dies. It is also possible to complete a die stress analysis using an uncoupled approach which provides multiple results such as the pressure loads, effective stress, maximal tensile stress and die deflection.
Would you like to receive information about other module offers?