Improving cold forming process using FEM simulation and automatic optimization techniques
Cold forming requires a good mastery of the process to give the expected output in term of part quality and shape control. As often, process difficulties have their counterpart in the simulation field.
- Manufacturing tolerances are very high and a predictive simulation tool has to give a result within these tolerances. It requires precision everywhere from material or friction model to meshing adaptation and updating marching scheme without forgetting matrix solving.
- People use complex dies sets and kinematic and of course, all that as to be taken into account in the simulation, increasing the number of coupled deformable bodies and the CPU time associated.
- Elasticity, in real life, may have a large influence through spring back phenomena and has to be carefully managed in simulation to avoid instabilities. In some processes, as incremental forming or thread rolling, the material is continuously moving from contact to free surface and the stresses grow and decrease many times.
- Residual stresses may be important and the remapping associated to the necessary re-meshing phases has to be done without too much diffusion.
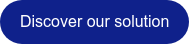
In the first part, we will illustrate how current difficult situations can be simulated using FORGE® or COLDFORM® software. The second part will be devoted to an example of cold extrusion process stability improvement using automatic optimization techniques. The third part describes the application of the Forge cold forming capabilities to the automatic optimization of self-aligning nut geometry.