Simulations of MIG MAG welding process with TRANSWELD®
MIG-MAG arc welding is one of the main welding processes used in industry and in particular in the automotive and construction sectors.
TRANSWELD® simulates and predicts the thermomechanical effects induced by the welding operation. It allows to preview the residual stresses, analyze the heat affected zones but also to study several forms of chamfer as well as various welding sequences with the aim of reducing expensive prototyping phases.
Assembly of two metal parts by arc welding process.
The simulation shows the temperature evolution while the deposit of three consecutive weld beads.
- With TRANSWELD®, you can quickly determine the optimum welding conditions for complex and quality assemblies.
Benefits of predictive simulation
TRANSWELD® allows you to predict:
- The behavior of the metal all throughout the process and in particular its solidification shrinkage
- The metallurgical transformations at solid-state induced by the welding operation, in particular in the HAZ
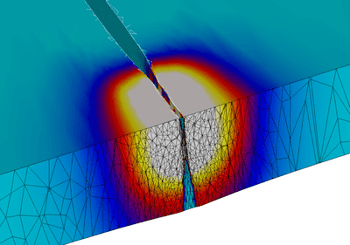
- The deformations induced by solidification and the welding sequence
- The residual stresses in the welded joint as well as the assembly distortions
- The penetration of the molten zone as well as any lack of fusion
- The shape of the weld bead obtained by adding material
- The capacity to test the mechanical resistance of the weld under conditions of use
Residual stresses in the welded joint
Competitive features of TRANSWELD® for Arc welding
Data setup based on the process parameters such as the voltage, wire speed, welding speed, the arc height, etc.
- Tool for preparing welded zones that has two computation modes:
- Mode in which the passes are predefined and pre-meshed, in the data setup in order to maintain a reduced computation time.
- Mode in which the chamfer is defined and the fusion of the metal is simulated so as to obtain a more precise solution, in particular concerning the penetration and lack of fusion.
- Tool dedicated to organizing the welding sequence including the management of the available torches, clamping and inter-pass conditions.
- Several coupling possibilities of physical phenomena (Thermal alone, Thermal and Metallurgy, Thermal and Metallurgy and Mechanical resolution) so as to balance computation time and type of result sought.
- Automatic remeshing technology allowing for an adaptation to the high gradient regions in order to improve the precision of the results by maintaining a reduced computation time.
- Complete welding solution allowing for preheating, post-heating and even thermal treatment of your welded assembly.