Numerical modeling can significantly contribute to innovation in the medical sector as it can serve different types of biomedical applications.
One example is Distraction OsteoGenesis (DOG). This is a surgical procedure that was mainly used in the field of orthopedics to reconstruct a deformed skeleton or to lengthen the bones of the body, especially the lower limbs.
This technique can be used for maxillofacial surgery. The advantage of DOG is that it can simultaneously increase bone length and the volume of surrounding soft tissues.
Original condition of the jaw with 2 incisors to be treated
These studies were conducted for Dr. Charles Savoldelli, (Maxillofacial surgeon in Nice) with a research version of FORGE® by CEMEF. The study took into account the interactions between bones, the cartilage layer and soft tissues.
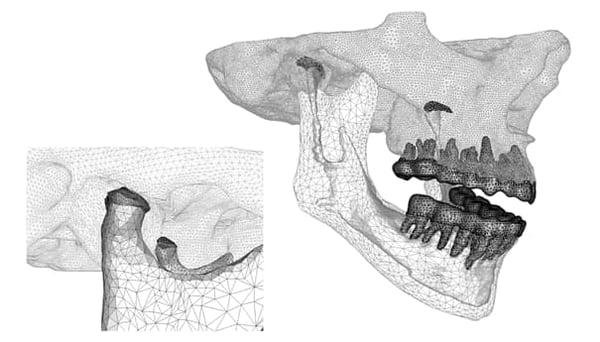
Implementation of the finite elements model (source Yannick Tillier, CEMEF)
Studying the interactions between bones, the cartilage layer and soft tissues
Characterization of biological materials
- Complex materials (heterogeneous, anisotropic, etc.)
- Environmentally sensitive materials
- Use of specific characterization equipment
- Use of reverse analysis for parameter identification
Numerical modeling
- Implementation of a hyper-elastic solver
- Complex geometry management
- Medical device design assistance (breast implants, heart valves, cochlear implants)
- Development of assisted surgery (gynecology, ophthalmology, maxillofacial)
Nature of results
- Stress distribution in the articular disks according to mouth opening
- Integration of patient asymmetry
- Impact of mechanical conditions and friction conditions applied between bones and/or tissues
Demonstration deformable multi-body calculus