Whether you do research, design or production, with the finite element software THERCAST® you reduce the time and cost to plan, optimize and virtually run your continuous casting process.
Transvalor THERCAST® is the best available solution to efficiently and accurately simulate your casting process, whether you want to optimize one that’s already in operation or to design a new one.
Model your continuous casting process from start to finish with THERCAST®. It accurately simulates the behaviour of your metal and every other element of the casting machine, including Electromagnetic devices, such as stirrers and brakes. All complex interrelationships between the various elements are taken into account.
With it you can optimize your casting speed or EMS parameters, prevent cracking and tearing, save energy, improve safety, and take other steps to increase quality and efficiency and reduce cost.
In this continuous casting example, THERCAST® simulates the entire process and all its complex interactions. The cooling effects of the secondary cooling rolls and sprays are clearly visible, together with radiation and air convection.
The digital twin of continous casting with Thercast®
Plant equipment designers and steelmakers all over the world have discovered the power, technical precision and flexibility of THERCAST® for a fully realistic and technically precise simulation of continuous casting. THERCAST® is the breakthrough tool to win all the challenges in the simulation of continuous casting.
Design and parameter optimisation for Electromagnetic dEvices
Simulation of M-EMS and brakes, S-EMS and F-EMS can 3D an be addressed with THERCAST® thanks to the new solver of the electromagnetic equations necessary to simulate the onset of a rotating magnetic field in the liquid metal and the consequent action of the Lorentz force field. The simulation provides full insights on the interaction of the magnetic field with the fluid flow and its effect of the formation of the solid skin, temperature distribution and related defects.
Thanks to the thermo-hydraulic simulation coupled with the electromagnetic solver, with THERCAST® you can achieve:
- Dimensioning of each component of the stirrer or brake
- Definition of appropriate current intensity and frequency of each device
- Precise assessment of the effect of Lorentz force on fluid flow and meniscus behaviour
- Positioning along the strand of S-EMS and F-EMS
Flow and thermal behavior of liquid steel in the tundish
Thanks to the versatility of its thermo-hydraulic model, THERCAST® can simulate the behaviour of a turbulent liquid in the ladle or the tundish at the top of the casting machine. It takes into account the behaviour of the free surface and gives the possibility to track inclusions and see the formation of gas bubbles. This way you will analyze:
- The paths and residence time of any inclusions within the liquid metal,
- The overall efficiency of the tundish, from a thermal and fluid-dynamic standpoint,
- Check new tundish design and practice
and you will improve the cleanliness of your product.
Studying trajectories taken by the fluid in a tundish
Simulation of mould, rolls and sprays
THERCAST® software accurately simulates in 3D the temperature, deformation, stress and other attributes of the metal during casting. Moreover it can compute the deformation and stress field of the mould and the mechanical and thermal interaction of the cast products with the rolls and sprays. This ability is unique to THERCAST®, and provides many cost, time and quality advantages.
You can :
- Optimize mold taper
- Predict the quality of the solid shell,
- Check bulging and avoid breakouts
This is possible thanks to Thercast® unique solver that is conceived to study complex phenomena like the interaction between the liquid metal and solid shell formation and shrinkage.
Left: Simulating the start of the continuous slab casting process (filling the cavity under turbulence).
Right: illustrating liquid metal paths and checking mold temperature using cooling channels during the process.
optimization of EMS and CASTING PARAMETERS
Thercast® is equipped with an automatic optimisation module which allows to expand the potential of simulation in achieving your goals.
As an example, casting speed is a critical parameter, and has to be set to a value which is a compromise between high productivity and profitability on one side and product quality and safety on the other. Moreover, its optimal value depends on the steel grade and on a number of other constraints coming from the process upstream and downstream the continuous casting. With the optimisation module you can explore in an efficient way the space of possible parameter settings to find the one which optimises your target function, whether it is productivity, product quality or a combination of both.
prevention of cracks and tears
Metal begins to cool and solidify as soon as it enters the mould, and this period of early solidification is extremely important in determining the integrity of the cast product. The fully coupled thermo-mechanical modeling in THERCAST® allows this phase to be studied because it is possible to simulate both the metal and the mould, their thermal and mechanical behaviour and the interaction between them, accounting for the effect of ferro static pressure, metal shrinkage and gap formation.
optimization of mould and cooling
THERCAST® can be used to design the optimum mould dimensions and cooling channels/gap, and secondary cooling system requirements, preventing guesswork or trial and error approaches and unnecessary expense. Whether you are designing copper plates for thin or conventional slab casing or thick tube moulds for high speed billet casting, THERCAST® is the tool for the functional and structural design of the moulds and of any coating applied to their surface.
mastery of MOULD taper
The solidifying steel shrinks as it moves from the meniscus to mould exit. Excessive air gap and non uniform contact between steel and mould can cause cracking and other defects. THERCAST® can predict this phenomenon with high technical precision: it is the right tool to design taper, also taking into account the deformation of the mould. Whether your mould is curved or straight, for standard or near-net-shape (funnel mould), for simple or complex profiles (beam blanks), you can try different taper profiles: linear, multi-linear or parabolic and visualise the consequent gap distribution for various steel grades and casting conditions: optimise the taper as a function of your productive mix.
Caption of picture: computed air gap projected onto the surface of the billet
energy savings
The integration of process and materials modelling in research, design and production is widely recognised to be critical for a more sustainable industrial development. This is particularly important in the steelmaking industry, one of the most energy-intensive industrial fields. THERCAST® being a powerful process-oriented simulation software, contributes to this green objective. For example it can help optimise the casting of products devoted to direct rolling, by determining the temperature distribution after the torch cut, determining the appropriate casting parameters to avoid/limit the use of additional reheating
Safety
Continuous casting is a large, complex, real-time undertaking in which problems can easily cascade and multiply, potentially with catastrophic results. Stresses and strains can produce cracking, tearing and even dangerous breakouts. With THERCAST®, your entire process can be modelled and operated as a simulation, allowing you to identify and prevent problems, long before physical setup and production start.
Computation method
A unique computation method, so-called Global Slice Computation (GSC), especially developed for THERCAST®, drastically reduces calculation times for continuous casting simulations. This method made it possible to simulate a 35-meter long strand 10 times faster than with the former method. LEARN MORE >
Case study: simulate soft reduction in continuous casting
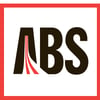
To conduct the revamping of a continuous casting machine, ABS Centre Métallurgique carried out simulations with THERCAST® software taking into account soft reduction.